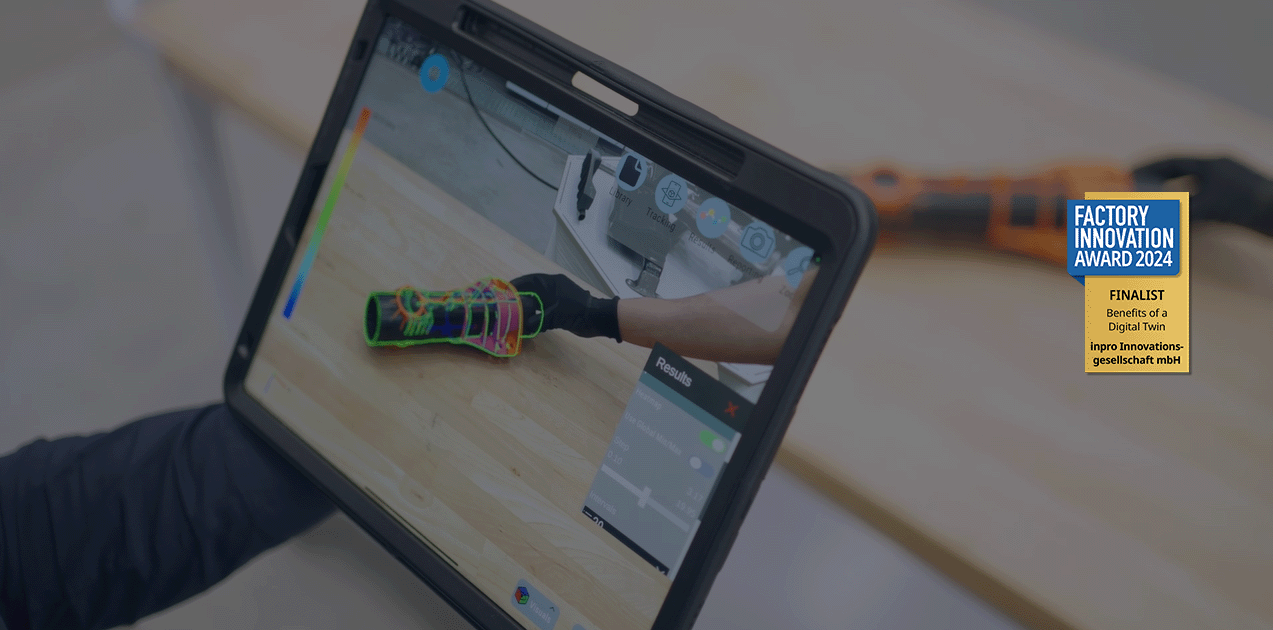
Adaptive Human-Machine Collaboration in the Injection Molding Industry
Injection molding has become a cornerstone of modern manufacturing, driven by continuous advancements in machine technology, material innovations—including multi-material molding—sensor integration, CAD/CAM systems, digital twins, and predictive maintenance solutions. However, despite these technological strides, injection molding processes often remain fragmented in practice. While the industry’s growth is largely fueled by the cost efficiency of mass production, significant opportunities for optimization still exist, particularly in the tryout phase.
In this article, we explore:
Aligning design engineering and shopfloor execution
To accelerate time-to-market through process efficiency, minimize material waste, and optimize costs while increasing production flexibility, seamless alignment between design engineering and shop floor execution is essential. Various solutions can facilitate this, such as equipping production facilities with sensors or integrating measurement technologies that relay production challenges back to CAD and simulation software. However, these approaches often involve high implementation effort and complexity, yet still fail to bridge the gaps in collaborative and iterative processes. Indeed, many companies continue to rely on Excel sheets to manage these information-intensive workflows.
With twino we have developed a smart and easy to implement solution that can fully align design engineering and shopfloor operations. twino integrates setup, inspection, measurement, and documentation functions to streamline the entire workflow. Unlike tools that address only isolated tasks, twino stands out as the only solution that seamlessly unifies these capabilities into a single, efficient system. By using twino, companies gain enhanced traceability, providing complete visibility into activities with suppliers and molders – eliminating the need to attend every trial in person. This level of traceability is invaluable for troubleshooting, as it delivers clear insights into any deviations from the original plan, enabling faster and more effective resolution. Operators can access the twino app on a mobile device, while design engineers use the synchronized desktop version to retrieve and leverage shop floor data within their Autodesk Moldflow-Software.
Mobile assistance systems in times of generational transition
Digitizing injection molding processes is not just about improving efficiency—it is also crucial for preserving implicit tryout knowledge within the company. In 2017, a quarter of the manufacturing workforce was over the age of 55, highlighting an impending skills gap. While existing teams may pose challenges to the much-needed digital transformation, onboarding a new generation of operators presents a valuable opportunity to systematically capture process expertise during the transition phase and drive incremental innovation. As AI disruption accelerates, technology will become more intuitive, making human-machine collaboration the new standard for leading injection molding companies. To support this shift, we are exploring chatbot interfaces that leverage natural language processing to streamline complex information management.
Discover more
Innovation table: Smart CAE robotics
With the Innovation Table "Automation & Robotics", inpro has set a central topic focus for partnership innovation projects in the coming years. CAE solutions for the planning of intelligent robotic systems are an elementary component of the digital factory of the future and at the same time a prerequisite for more sustainable automotive manufacturing.
Multirobot cell planning 2.0
ginero is a plugin for Process Simulate for the planning and virtual validation of multi-robot cells. With the latest release, the complexity for system planners has been significantly reduced once again.