
Closing the Loop between Engineering and Production
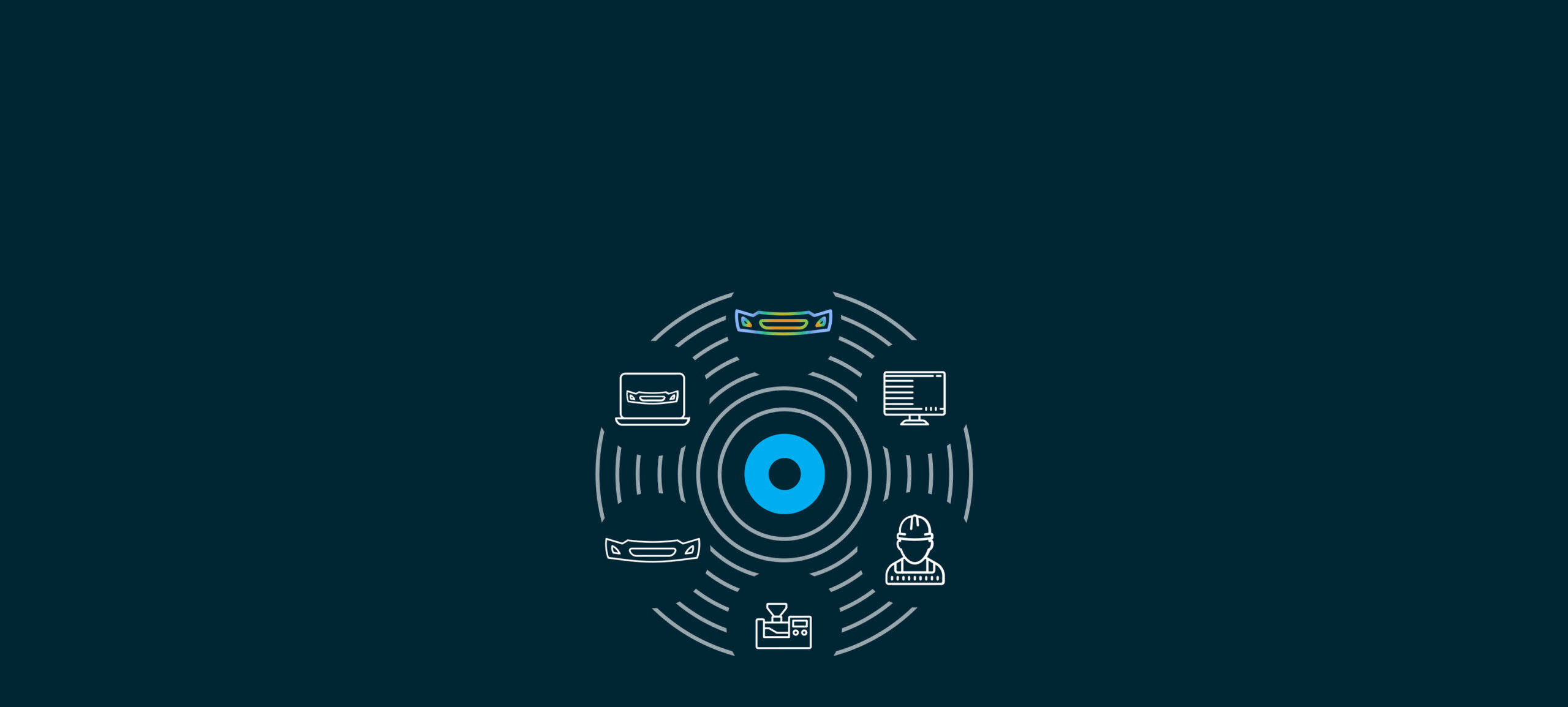
Closing the Loop between Engineering and Production
Close the loop between simulation and reality
Efficient and easy inspection
Faster collaboration along the value chain
twino supports your tryout workflows to speed up time to start of production
Overview of twino Functions & Features
What our customers say
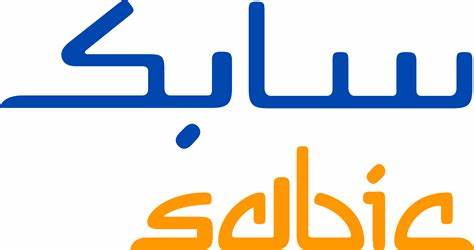
“SABIC believes collaboration is a must-have, not a maybe. That’s why we are excited about twino and the potential it has to be a game changer for collaboration between and among engineering and shop floor production teams. We were pleased to be one of the partners who helped inpro bring twino to life, and we look forward to keeping using this technology to demonstrate the value of our advanced predictive engineering capabilities.”