
Digitale Entwicklung & Produktion zusammenführen
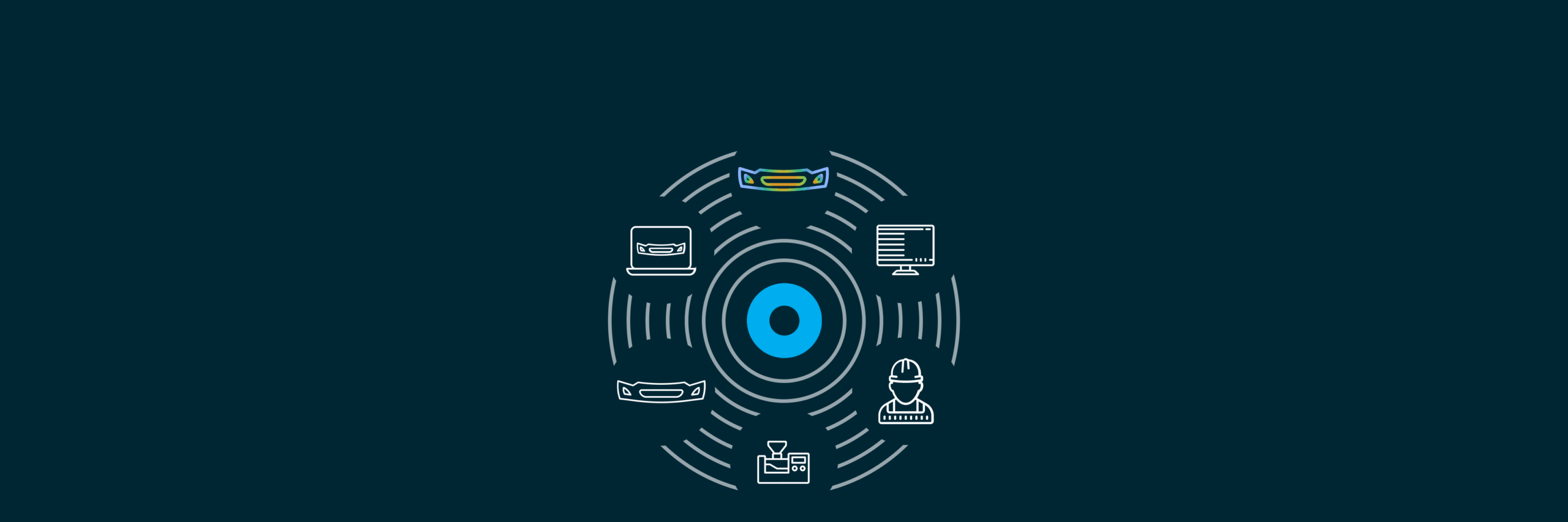
Digitale Entwicklung & Produktion zusammenführen
Schließen Sie die Lücke zwischen Simulation und Realität
Effiziente und einfache Prüfabläufe
Effektive Zusammenarbeit entlang der Wertschöpfungskette
twino verkürzt die Zeit bis zum Produktionsstart durch smarte Tryout-Workflows
twino Funktionen & Features im Überblick
Was unsere Kunden sagen
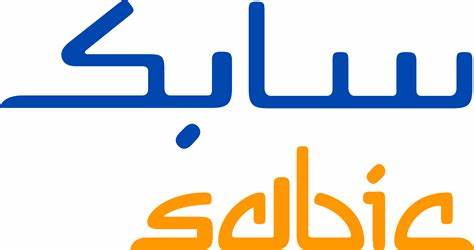
„Zusammenarbeit ist ein Muss, nicht ein Vielleicht. Deshalb sind wir begeistert von twino und dem Potenzial, das es hat, die Zusammenarbeit zwischen und unter den Entwicklungsteams und den Produktionsteams in der Fertigung zu verbessern. Wir freuen uns, einer der Partner zu sein, die inpro dabei geholfen haben, twino zum Leben zu erwecken, und werden diese Technologie weiterhin nutzen, um den Wert unserer fortschrittlichen Predictive Engineering-Funktionen zu demonstrieren.“
twino FAQs
Produktübersicht
Nutzung in der Praxis
Zukunftsausblick