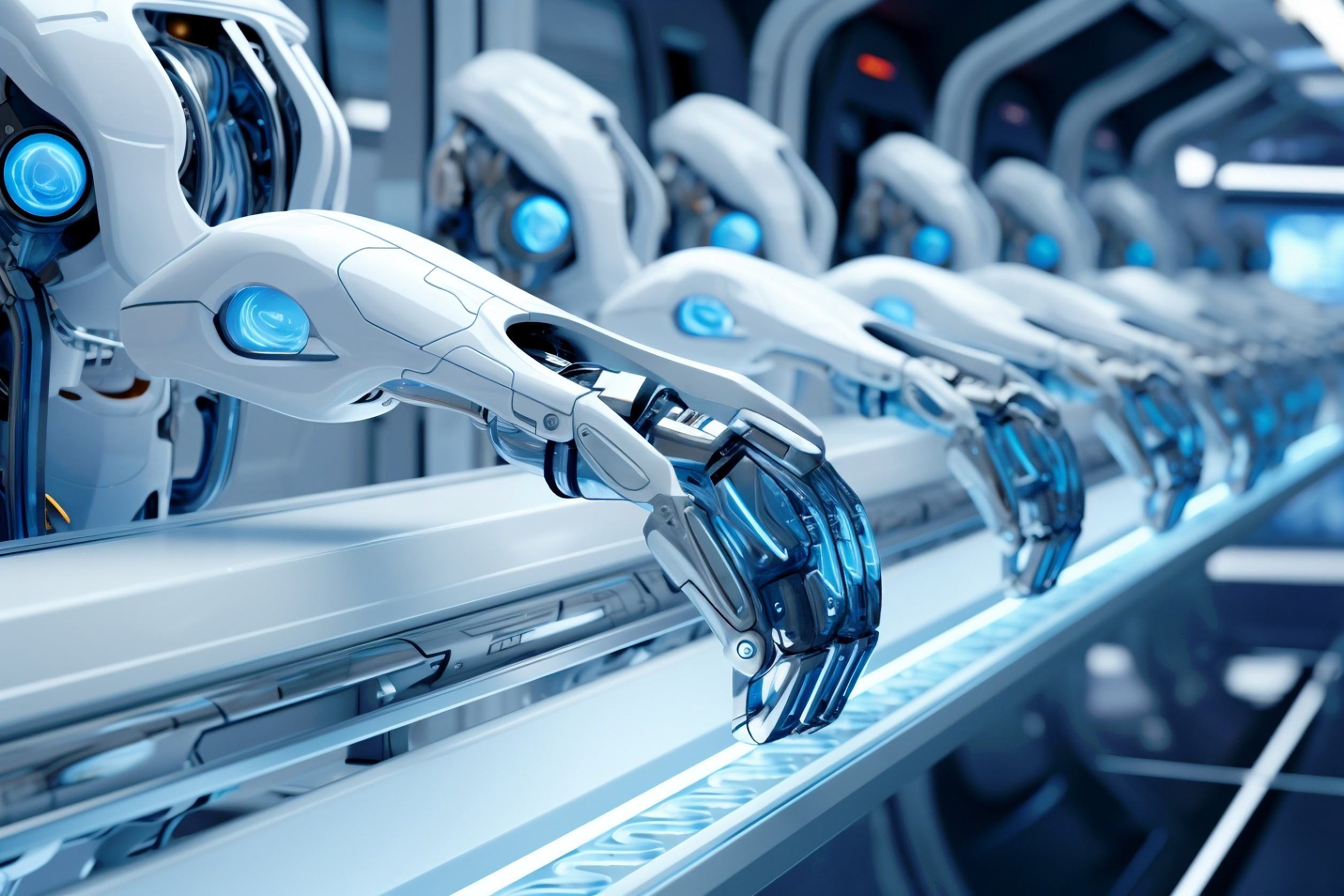
Robotics 4.0 in focus
Robotics trends 2030: Flexibility in automation
According to the latest report from the International Federation of Robotics, computer vision is one of the most important drivers of innovation in modern robotics after artificial intelligence. The average annual growth rate of this technology is 18%. Mordor analysts forecast a market volume of 40 billion US dollars for the year 2029. Other robotics trends such as mobile manipulators and the digital twin cannot be viewed in isolation from modern sensor technology and machine vision. Together, these technologies contribute to intelligent, autonomous industrial robots and can address challenges such as the shortage of skilled workers and cost pressure in a solution-oriented manner.Fast progress in digitalization and investments can currently be observed in robot-assisted handling, as e.g. in order picking systems in logistics.
Manual vs. automated parts handling in automotive production
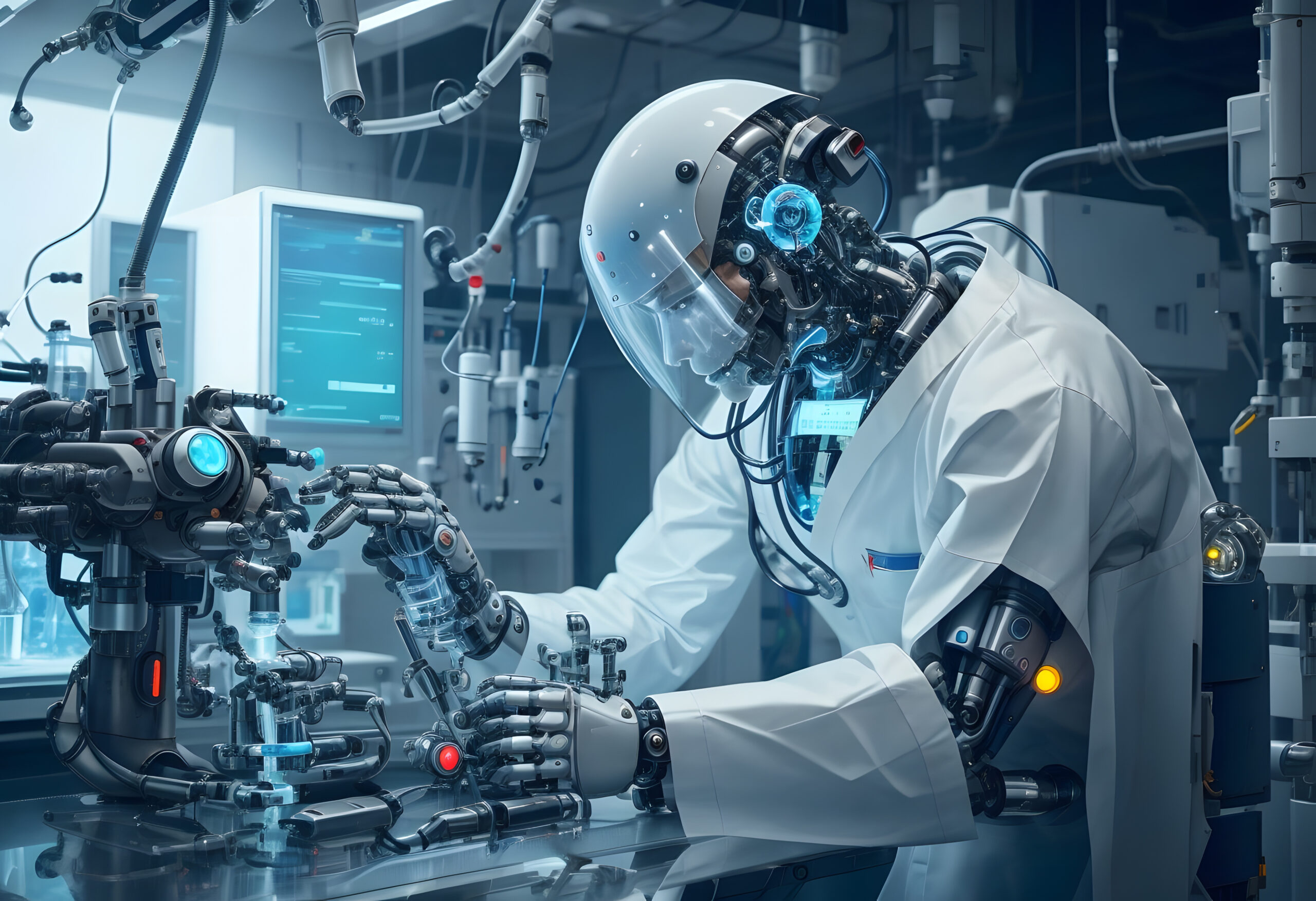
Machine learning of computer vision robot systems
The establishment of vision systems in the manufacturing industry
While the layout planning of production cells and the offline programming and validation of robots is still carried out as standard today without the special integration of image processing systems, we assume that this will be an integral part of the planning phase in the near future. Several technological trends are helping to ensure that this combination for safeguarding computer vision robots in engineering will quickly become established and that nothing will stand in the way of these systems becoming established on the store floor. In detail, these are
Collaborative Incubation: Membership model for industrial innovators
Discover more
We are a Siemens Solution Partner
We are part of an international competence network in the Siemens partner ecosystem that is constantly adapting to new requirements and technologies, helping to develop and refine them and is thus ready for the automation tasks of the future.
Technology monitoring as a competitive advantage
In this blog post, you can read how you can use our technology intelligence solution texploro to conduct structured competitive and R&D analyses, and what we are currently working on to make your search results even more effective.